Full Core Restoration
Restore Core Integrity And Maximize
Efficiency Of Your Engines
What to Expect From A Full Core Restoration
A full core restoration on a CFM56 engine involves an extensive and meticulous process to bring the engine’s core components back to their original performance standards.
This restoration typically includes a complete disassembly of the engine. It is then followed by detailed inspection and testing of the core elements. These elements include the high-pressure compressor, combustor, high-pressure turbine, and related components.
During the restoration, any worn or damaged parts are repaired or replaced. This ensures that the engine meets or exceeds manufacturer specifications.
Critical processes such as precision machining, coating, and balancing are employed to restore the core’s integrity and efficiency. Once reassembled, the engine undergoes rigorous testing to verify its performance and reliability.
The full core restoration process not only extends the life of the engine but also optimizes its fuel efficiency and operational safety. Also ensuring it is fully ready for service.
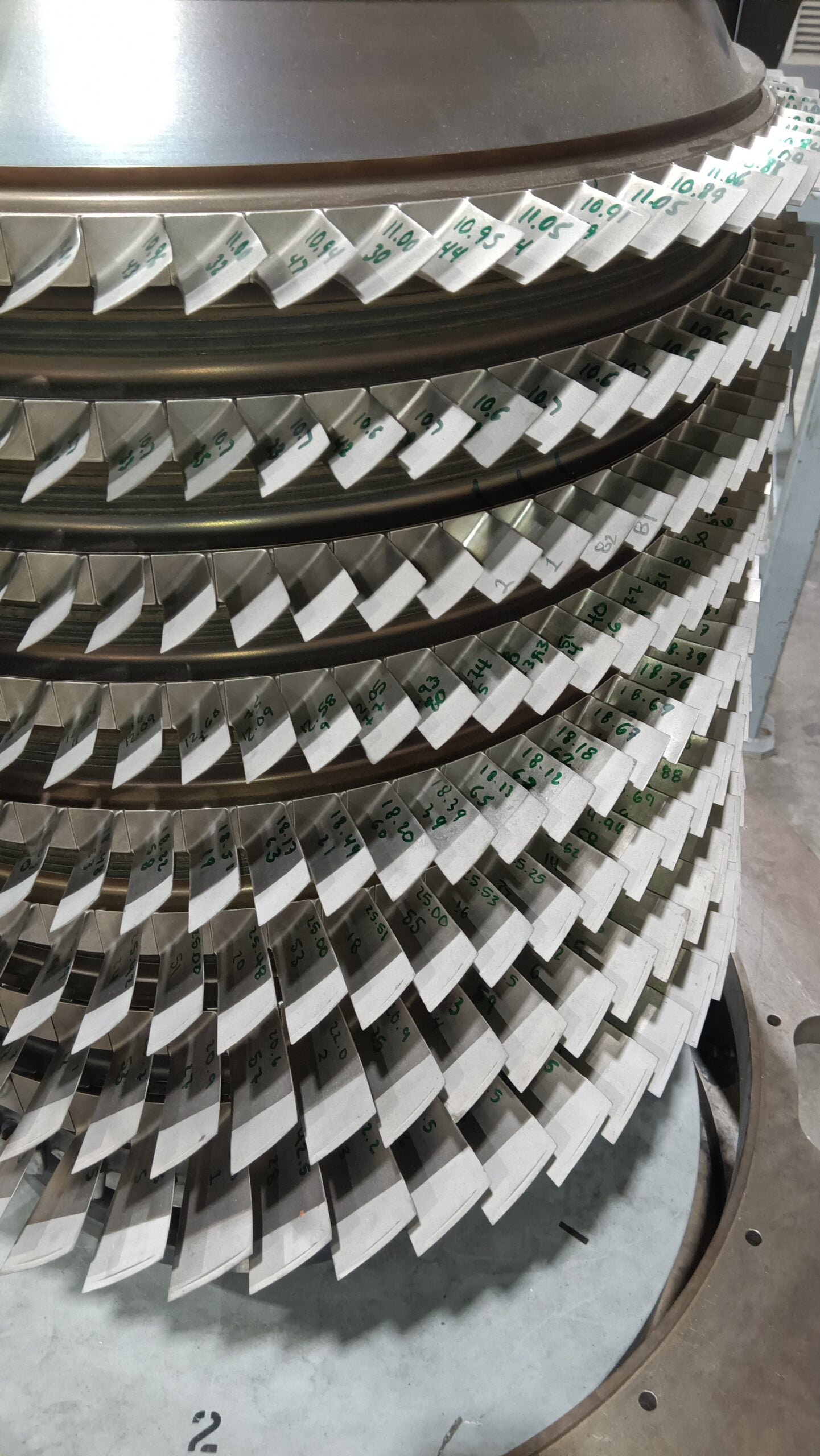
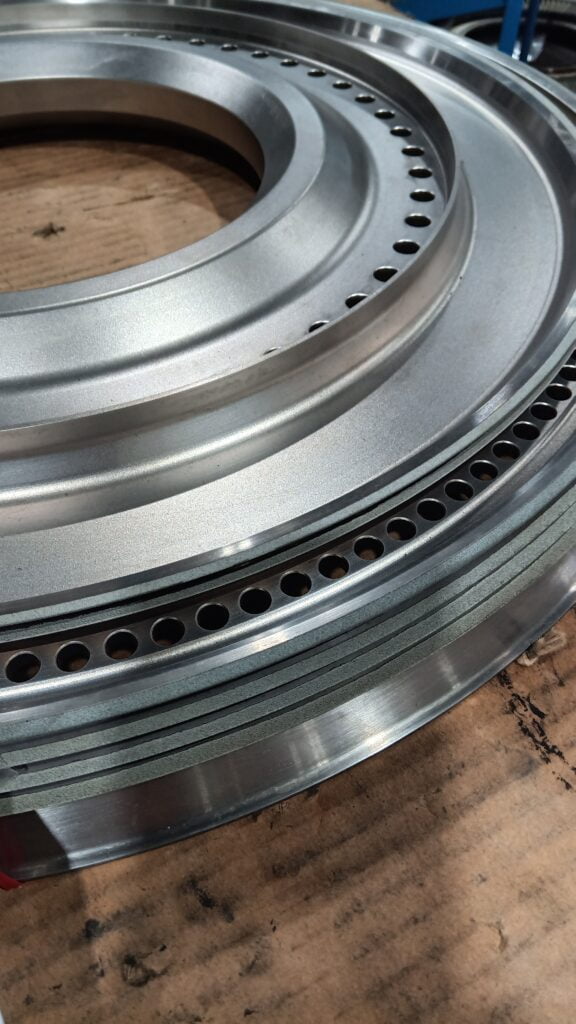
Full Core Restoration Process for a CFM56 Engine
How It’s Done:
- Initial Disassembly: The process begins with the complete disassembly of the engine’s core, including the high-pressure compressor (HPC), combustor, and high-pressure turbine (HPT). Each component is carefully separated for individual inspection.
Detailed Inspection: Every core component undergoes thorough inspection using advanced techniques like borescope inspections, non-destructive testing (NDT), and precision measurement tools. This helps identify any wear, cracks, corrosion, or other defects.
Component Repair and Replacement: Damaged or worn components are either repaired or replaced with OEM-certified parts. This can involve processes such as welding, machining, re-coating, and rebalancing of the core components.
Cleaning and Surface Treatment: All core parts are cleaned to remove debris, contaminants, and oxidation. Surface treatments, such as thermal barrier coatings or corrosion-resistant coatings, may be applied to protect the parts from future wear.
Reassembly: Once the components are restored, the engine is meticulously reassembled with precise alignment and torque specifications to ensure all parts fit together correctly and function as intended.
Testing and Validation: After reassembly, the engine undergoes comprehensive testing, including a performance run on a test cell. This step verifies that the engine meets all operational parameters, such as thrust output, fuel efficiency, and temperature limits.
Final Inspection: A final inspection ensures that all work has been completed to the highest standards, with documentation and certification provided for regulatory compliance.
Got questions? We’ve got answers.
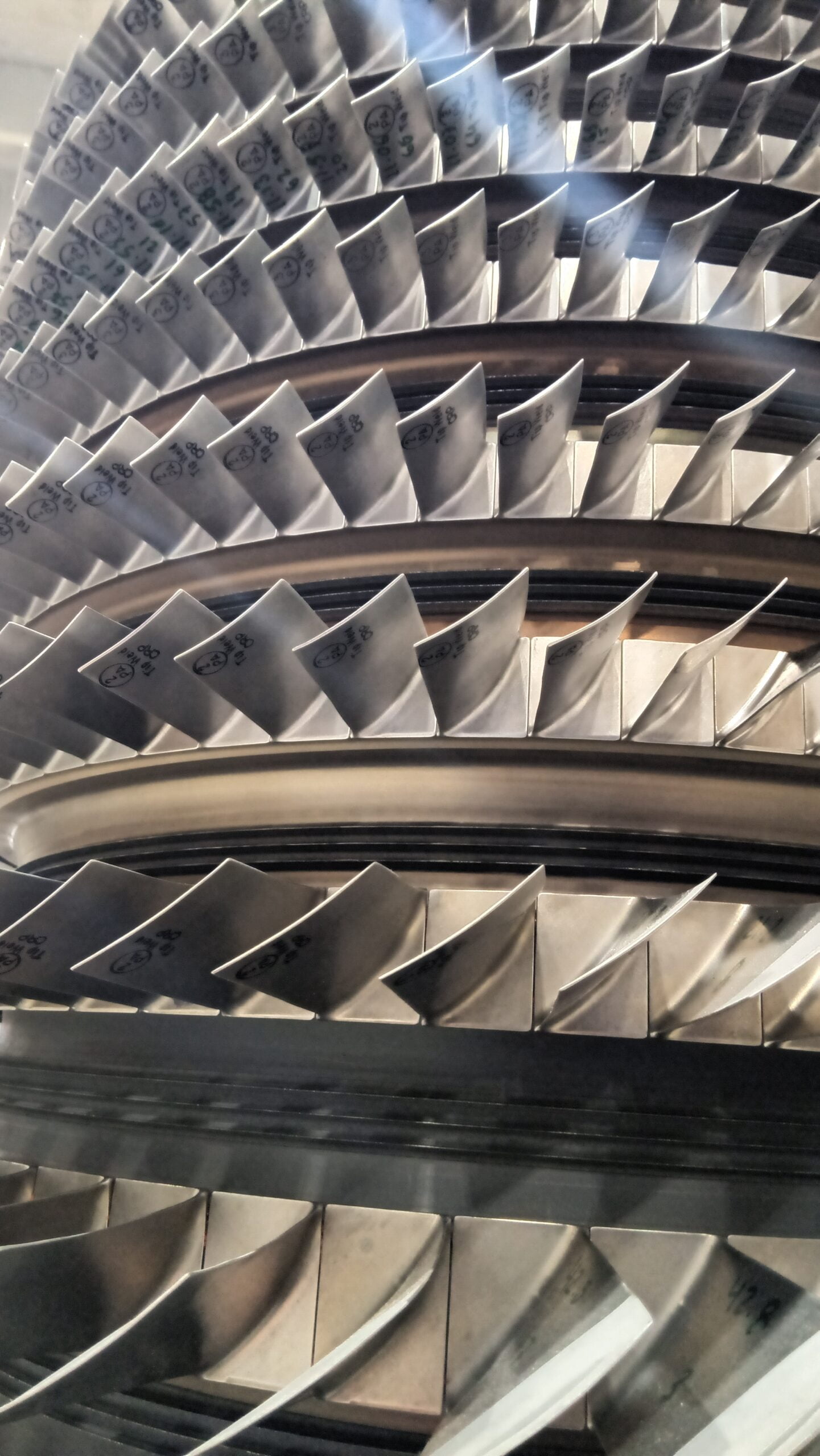
Expected Results
Restored Performance: The engine’s performance is restored to like-new condition, with optimized thrust, fuel efficiency, and overall reliability.
Extended Service Life: The restoration significantly extends the engine’s service life, reducing the need for frequent repairs and increasing time between overhauls (TBO).
Enhanced Safety: The engine is thoroughly tested to ensure it meets or exceeds safety standards, providing peace of mind for operators and crew.
Improved Fuel Efficiency: By restoring the engine to its original specifications, fuel consumption is optimized, leading to cost savings in operation.
Regulatory Compliance: The engine is certified to meet all relevant aviation regulations, ensuring it is fully compliant and ready for service.